In 2019, the U.S. generated nearly seven million tons of electronic waste, only 15% of which was recycled. The rest ended up in landfills. According to Earth911.com, a recycling database, the value of the raw materials contained in this unrecycled e-waste was approximately $7.49 billion. This waste of costly materials isn’t just bad for the planet, it’s bad for business too, and companies are taking notice. E-waste recycling has long been important to a company’s image, but now there are real financial benefits as well.
Today, electronics manufacturers are taking steps to claw back useful materials from their discarded electronics, helping both the environment and their bottom line. Several major manufacturers now accept expired electronics for recycling, including Apple, Dell, Microsoft, and Samsung. And all these manufacturers have programs in place that allow them to benefit from almost every stage of the recycling process.
Refurbish and Resell: The Easiest Type of E-Waste Recycling
Both Apple and Dell allow customers to trade in their old devices when they buy a new one. Consumers get a modest credit to put towards a new device, and the manufacturers get a product they can refurbish and sell at a profit. Of course, some of these devices are so out of date that they can’t be refurbished. In this case, the consumer doesn’t earn any credit towards a new device, but most customers still feel good about turning in the product for recycling, and this generates a sense of goodwill towards the manufacturer.
Take-back programs benefit both consumers and the environment. They also boost the corporate image of the electronics manufacturers who run these programs, since by refurbishing electronic devices for resale, these companies can rightfully claim that they’re helping to ease the strain on landfills. And now, thanks to improving technology and innovative revenue-sharing programs, e-waste recycling programs are also benefitting the profit margins of these electronics manufacturers.
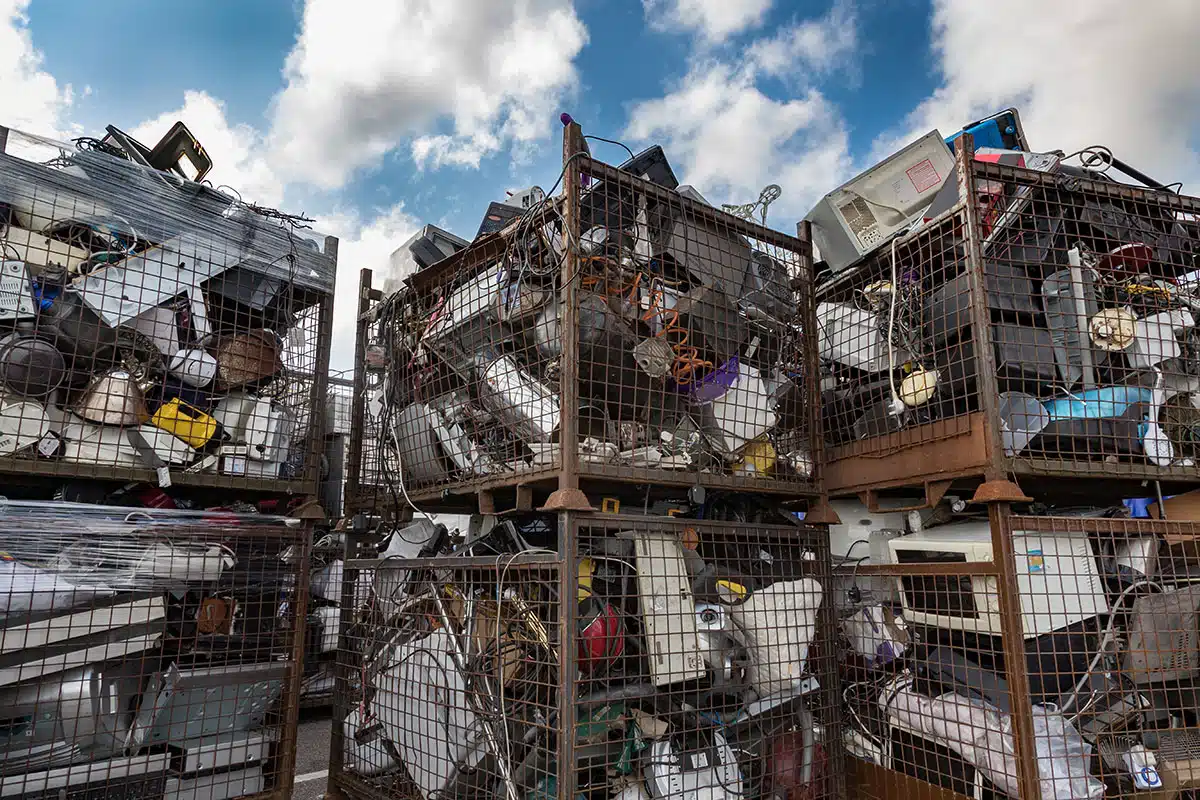
Repurposing Components
Not every device that gets turned in for recycling can be updated and resold. In these instances, manufacturers partner with an e-waste recycler to recapture some of the value of these used electronics.
The first step in recycling an electronic device is to pull out those components that can be repurposed “as is.” All the major recyclers harvest usable components from old electronic equipment before sending the leftovers to be recycled. Keyboards, screens, hard drives (wiped clean, of course), processors, memory units, and motherboards can all be given a second life in a new device.
It takes time and skill to remove an individual component from an electronic device. And then the recaptured part must be cleaned, checked for functionality, and packaged for sale. But the labor-intensive effort is worth it. A server’s hard drive, for example, can fetch $300 on the secondary market.
And where are these hard drives, motherboards, and other parts sold? Most go to wholesalers, but if you shop for electronics components on eBay, you may have bought one of these repurposed parts.
Large recyclers have revenue-sharing arrangements with their Fortune 500 customers, in which both parties split the proceeds from the sale of these repurposed parts. In this way, electronics manufacturers continue to capture value from their products, even at the end of their lifecycle.
Extracting Raw Materials
Some electronics components, like smaller hard drives, simply can’t be repurposed. These pieces get broken down and shredded, along with the shell of the original electronic device. At this stage, electronics manufacturers don’t typically benefit directly from the recycling process, but the indirect gains are substantial.
In addition to batteries, electronic components contain a lot of hazardous elements, like mercury, cadmium, and lead. And when electronic devices don’t get recycled, these elements end up in landfills, where they leach into soil and ground water. Take-back programs like the ones run by Apple and Dell let these companies credibly claim that they are doing their part to reduce the amount of hazardous materials in the environment.
And there are financial benefits as well. According to the United Nations, more than $10 billion of precious metals is dumped each year in the world’s electronic waste. “Losing” metal in this way drives up the cost of making new electronics. Diverting electronics from landfills and reusing the essential components keeps valuable metals from being wasted, which has a dampening effect on their cost.
And there’s another trend that’s sure to lower the cost of these key raw materials. Scientists have been busy finding ways to extract precious metals from recycled e-waste.
Recovering Precious Metals
According to the Environmental Protection Agency, one metric ton of circuit boards can contain 40 to 800 times the amount of gold and 30 to 40 times the amount of copper mined from one metric ton of ore in the U.S., which means some landfills have higher concentrations of precious metals than typical mining facilities. Traditionally, extracting gold and other metals from electronics has been a laborious process, which is why right now only about $4 billion of precious metals are recaptured from e-waste every year.
But a new process, developed by engineers at Rice University, is changing the extraction landscape. The technique involves grinding up electronics and then flash-heating them with a zap of electricity to vaporize the metals. The metallic gases are then vented away into separate chambers, where they coalesce back to their natural state as they cool.
According to a 2021 article in ScienceDaily, this new extraction method uses 500 times less energy than traditional methods, and produces a byproduct that’s “clean enough for agricultural land.” This new development reduces the need for hazardous and polluting mining operations while increasing the availability of precious metals, thus lowering their cost. It also encourages the recycling of electronic waste, even if that e-waste is already sitting in a landfill, a development that leads ScienceDirect to predict a rise in “urban mining.” As one of the scientists who developed the technique says, “The treasure is in our dumpsters.”
This is good news for companies that rely on rare earths and precious metals to build their products, especially electronics manufacturers, who gobble these metals at a high rate.
Making Plastic Cheaper through E-Waste Recycling
After an electronics product has been fully “demanufactured” and had all its valuable and/or hazardous components removed, everything that’s left of the original product—mostly plastic and some metal—gets shredded. After this material is shredded, large magnets pull metal from the debris as it passes on a conveyor belt, leaving only plastic, which will be further processed in a plastics compounder, then shipped to an electronics manufacturer and used to make new products.
Modern techniques have brought down the price of recycled plastic, but even so, right now recycling the type of plastic used to make computers and other electronics is an extremely difficult process. That’s because, unlike a soda bottle, which is made of a single polymer, the plastic used for electronic products is made of a complex polymer blend, which makes it difficult to recycle.
But a recent development bodes well for a further drop in the cost of recycled plastic. Researchers at the Illinois Sustainable Technology Center have discovered a nontoxic solvent that can recover polycarbonates, a group of thermoplastic polymers found in the plastic components of many electronic devices. The hope is that once the technology becomes more widespread, recycling a phone case will be as easy as recycling a soda can. It will also be easier to turn phone cases into soda bottles, and vice versa. This is great news for electronics manufacturers, who use more than 10 million tons of plastic every year.
Looking Towards the Future
E-waste recycling benefits electronics manufacturers financially, and generates customer goodwill. Given these benefits, electronics companies can gain further advantages if they make their products easier to recycle. Fortunately, there are several steps that manufacturers can take to achieve this.
According to the European Commission, 80% of a product’s environmental impact is determined by its design. A product’s design determines the raw materials used, the amount of energy the product will consume over its lifecycle, and how easily the product can be recycled at the end of its life. Designing products to reduce the amount of hazardous materials used will make the resulting product easier to recycle.
Another way to support easy recycling is to make individual components easier to reach. Some electronics devices are like black boxes, sealed tight with glue and proprietary screws. This not only frustrates consumers—hence the rise in “right to repair” laws—it also makes recycling unnecessarily arduous. That’s one reason why companies like Dell are changing the design of their products, making them easier to open up.
Building an E-Waste Recycling Program
Electronics companies looking to squeeze more revenue from their existing product lines should take a look at their recycling options. A comprehensive take-back program can create a reliable revenue stream, through both whole product and component resales. And the benefits of recycling are more than just monetary.
Now more than ever, consumers pay attention to a company’s ecological footprint. A 2022 study in ScienceDirect found that consumers not only prefer greener products, they also perceive these products as being of higher quality. Committing to the use of recycled materials, and making it easier to recycle discarded electronics, can cement a company’s reputation as a green leader. A well-planned, well-publicized e-waste recycling program brings far-reaching PR benefits to any company.